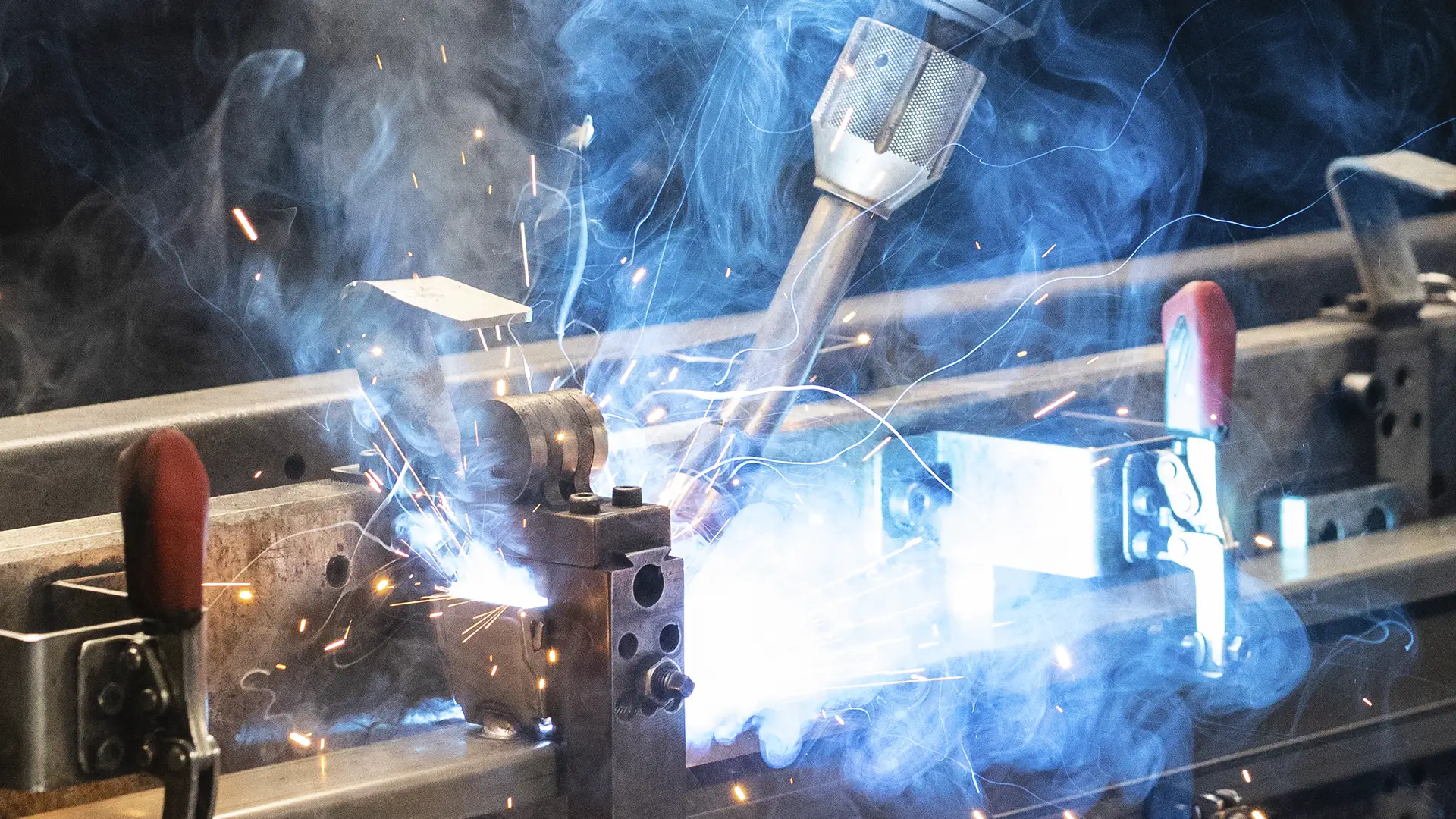
You’ve probably seen videos on social media showing the impressive capabilities of laser welding. It’s real, and JOM is already equipped with this technology! Here’s an explanation of the applications and advantages of this industrial process:
Laser welding is a cutting-edge technology revolutionizing the metalworking industry through its precision, speed, and versatility. This welding method uses a highly focused laser beam to fuse metallic materials, providing a range of benefits that make it especially suitable for producing high-quality metal components, like those manufactured by JOM METAL PARTS MANUFACTURING, S.L.
Main advantages of laser welding compared to traditional methods
1. High Precision and Weld Quality
Laser technology allows precise control over the welding point, resulting in cleaner and higher-quality joints. Thanks to its precision, laser welding is ideal for working with delicate parts or complex geometries, and its focusing ability allows welding specific points without damaging surrounding areas. This translates to superior aesthetic finishes and greater structural integrity of the parts.
2. High Processing Speed
Laser welding is significantly faster than traditional welding methods, increasing productivity. This speed is due to the laser’s high energy concentration, which can weld materials in less time. Speed is a key advantage in automated production lines and large series, where optimizing processing time without sacrificing quality is essential.
3. Application on Thin and Delicate Materials
Laser welding is particularly advantageous for working with thin materials like aluminum or stainless steel, which can easily deform under heat. Thanks to the laser’s thermal control, these materials can be welded without compromising their integrity or causing distortions. This factor is crucial in manufacturing parts that require precision and care, minimizing the need for rework and adjustments.
4. Reduction of Deformations and Distortions
Since the laser applies heat in a localized manner, the heat-affected zone is minimal. This reduces the amount of stress and deformation in parts during the welding process, an important advantage for high-precision components or those that need to be assembled later without losing alignment. Minimal deformation also reduces the need for post-weld rectification processes.
5. Automation Capability
Laser welding is easily integrated into automated production systems, which is ideal for series manufacturing. This method combines the precision and speed of the laser with the efficiency of automation, optimizing production times and reducing human error. Additionally, the laser can be controlled remotely and parameters adjusted for a more flexible and repeatable process.
6. High-Strength and Durable Welds
Laser technology allows for deep and strong welds, which is essential in industries that require high durability for their products. Laser welding provides joints that can withstand high stress and extreme conditions without premature deterioration, ensuring high performance and longevity of parts.
Conclusion
Laser welding offers a range of advantages, making it a top choice for manufacturing metal components, especially in sectors where precision, speed, and durability are essential. At JOM METAL PARTS MANUFACTURING, S.L., we leverage this advanced technology to deliver high-quality products, optimizing our production processes and ensuring client satisfaction. Laser welding not only improves efficiency but also sets new standards for quality and reliability in the metalworking industry.