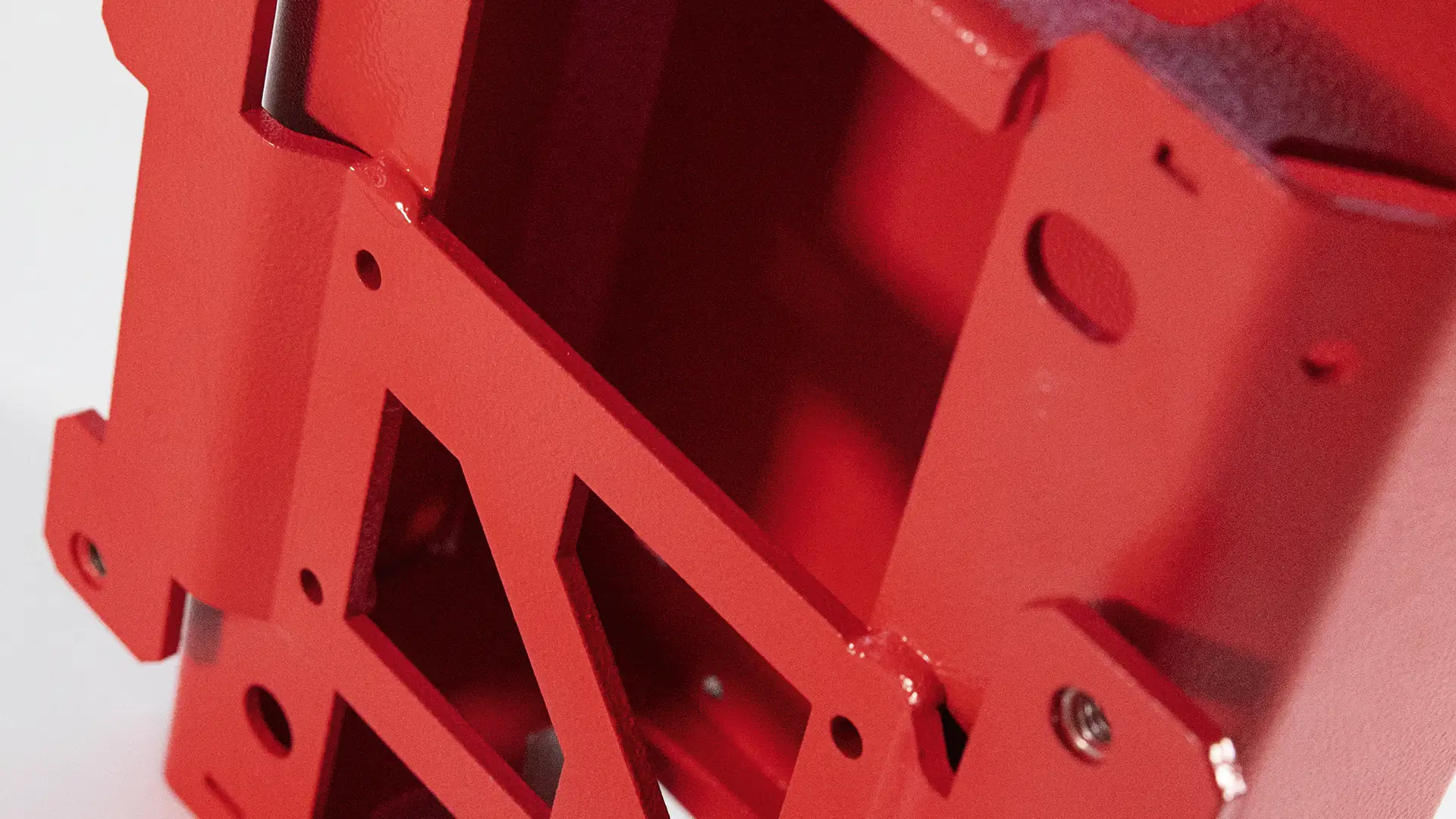
Surface Treatments for Sheet Metal: Options and Benefits
Surface treatments for sheet metal are essential in metal parts manufacturing as they not only extend the product lifespan but also improve performance and aesthetics. Each treatment provides specific properties, such as corrosion resistance, increased hardness, or a decorative finish, adapting the sheet metal to various industrial applications.
Main Surface Treatments for Sheet Metal
Below, we explore some of the most popular surface treatments in the metal parts manufacturing industry:
-
Galvanizing
Galvanizing is one of the most popular treatments for metal parts exposed to humid or adverse environments. It consists of applying a layer of zinc on the sheet surface, acting as a protective barrier against oxidation. This process allows the zinc to oxidize before the base metal, thus extending the part’s lifespan. It is a durable and low-maintenance option, ideal for construction structures, fences, and parts exposed to the elements.
-
Zinc Plating
Zinc plating, also known as electrolytic zinc coating, is done through an electrochemical bath that creates a thinner and more uniform layer of zinc compared to galvanizing. This treatment is ideal for parts requiring corrosion resistance and an attractive finish. Additionally, it allows for different color finishes, making it suitable for sectors where appearance is key, such as automotive and decoration.
-
Powder Coating
Powder coating, or electrostatic coating, is a dry coating applied through static electricity and then cured in an oven. This treatment provides a uniform and durable layer, ideal for improving both the durability and aesthetics of the part. It offers a variety of colors and textures and is less polluting than conventional liquid paints, being widely used in the automotive and appliance sectors.
-
Electrolytic Treatments
Electrolytic treatments, such as nickel plating and chrome plating, involve immersing parts in a solution of metallic ions, which are deposited on the sheet under an electric current. These processes improve corrosion resistance, increase surface hardness, and offer a decorative finish, such as a metallic shine or a satin finish. They are ideal for parts requiring additional protection and an attractive finish.
-
Quenching
Quenching is a heat treatment that involves heating the metal to high temperatures and rapidly cooling it. This process increases the hardness and resistance of the sheet metal, making it suitable for components subjected to mechanical stresses or continuous wear. Quenching is particularly useful in high-demand applications, such as machinery components and tools.
-
Passivation
Passivation is a chemical treatment that creates a protective oxide layer on stainless steel and other metals. This layer is highly resistant to corrosion, helping to extend the metal’s lifespan. Passivation is particularly useful in environments with exposure to chemicals or high humidity, minimizing the risk of oxidation without affecting the piece’s finish, making it ideal for medical and food sectors.
-
Anodizing
Anodizing is an electrolytic treatment that converts the aluminum surface into a layer of aluminum oxide, improving its resistance to corrosion and wear. Additionally, anodizing allows for decorative finishes in different colors, making it ideal for parts that require durability and aesthetics. It is commonly used in sectors such as architecture and automotive.
Frequently Asked Questions (FAQ)
What is the best treatment to prevent corrosion in metal parts?
Galvanizing and zinc plating are popular options for protecting metal parts against corrosion. Anodizing is also ideal for aluminum parts that require additional protection.
What is the difference between galvanizing and zinc plating?
Galvanizing applies a thicker layer of zinc through hot-dipping, while zinc plating creates a thinner and more uniform layer through an electrochemical bath, ideal for parts with aesthetic requirements.
What are the advantages of powder coating over other types of paint?
Powder coating offers a more durable, uniform, and eco-friendly layer compared to liquid paints. Additionally, it allows for a variety of colors and textures.
Interested in enhancing the durability and aesthetics of your metal parts?
At JOM, we have extensive experience in advising and applying surface treatments for sheet metal. We understand that each project has unique requirements in terms of usage conditions, aesthetics, and durability, so we work closely with our clients to identify the most suitable solutions.
We handle these treatments with certified providers in our industrial area, ensuring the highest quality and compliance with industry standards.
Feel free to contact us for specialized advice and a personalized quote. At JOM, we are committed to offering high-quality solutions that maximize the performance of your products.